[Automatic high frequency welder]Exploring the Efficiency and Advantages of the Automatic High Frequency Welder in Modern Manufacturing
In the landscape of modern manufacturing, the need for reliable and efficient welding methods is more critical than ever. Companies are constantly seeking innovative solutions to enhance productivity, improve product quality, and reduce operational costs. Among the various welding technologies available today, the automatic high frequency welder stands out as a particularly effective solution. This advanced technology leverages the principles of high-frequency electromagnetic waves to create strong, durable welds in a fraction of the time required by traditional methods. This article delves into the characteristics, benefits, and applications of automatic high frequency welders.
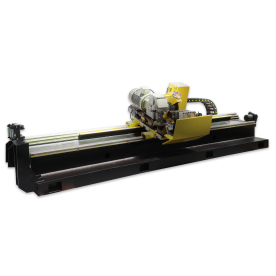
Exploring the Efficiency and Advantages of the Automatic High Frequency Welder in Modern Manufacturing
Understanding Automatic High Frequency Welding
Automatic high frequency welding is a process that utilizes high-frequency electromagnetic energy to generate heat at the surface of materials to be welded. This technique is primarily used for welding thermoplastic materials and certain metals, allowing them to be joined quickly and efficiently. The welding is achieved by placing the materials in close proximity and applying the high-frequency energy, which causes the surfaces to melt and fuse together when pressure is applied.
The automation aspect of this technology refers to the integrated systems that control the welding process. These systems often include programmable logic controllers (PLCs) and human-machine interfaces (HMIs), allowing operators to set specific parameters, monitor the welding process in real-time, and adjust settings as needed without manual intervention. This automation significantly reduces the risk of human error and enhances the consistency of the welds produced.
Advantages of Using Automatic High Frequency Welders
1. **Efficiency and Speed**: One of the most significant advantages of automatic high frequency welders is their operational speed. The welding process is incredibly fast, allowing for high throughput in a manufacturing environment. This is particularly beneficial for industries needing to produce large quantities of products in a short time frame, such as automotive manufacturing and packaging industries.
2. **Quality and Consistency**: The precision offered by automatic high frequency welding technology results in high-quality welds that meet stringent industry standards. The automation ensures that each weld is produced under the same conditions, minimizing the chances of defects. This increased consistency is crucial for applications where safety and reliability are paramount.
3. **Versatility**: Automatic high frequency welders can handle various materials, including plastics, metals, and composite materials. This versatility makes them suitable for a wide range of applications, from fabricating medical devices to manufacturing automotive components. Regardless of the substrate, high-frequency welding can create strong joints that can withstand significant stress and strain.
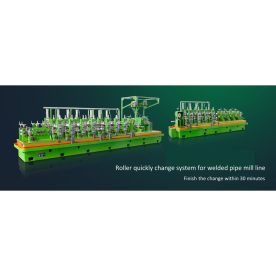
Exploring the Efficiency and Advantages of the Automatic High Frequency Welder in Modern Manufacturing
4. **Reduced Waste**: Traditional welding processes often result in considerable material waste due to burn-through or ineffective joint formation. Automatic high frequency welding minimizes this waste because the process is focused and controlled, leading to cleaner, more efficient operations. This not only conserves materials but also translates into cost savings for manufacturers.
5. **Enhanced Safety Features**: Many automatic high frequency welders come equipped with safety mechanisms, such as emergency stop buttons and sensor systems, that protect operators from accidents and injuries. By reducing the amount of manual intervention required in the welding process, the risk of human error is lessened, enhancing overall workplace safety.
Applications in Various Industries

Exploring the Efficiency and Advantages of the Automatic High Frequency Welder in Modern Manufacturing
Automatic high frequency welders find applications across numerous sectors due to their efficiency and versatility. In the automotive industry, they are used to weld components like fuel tanks and exhaust systems. In the packaging sector, these welders are employed to create strong seals in plastic packaging, ensuring product integrity and extending shelf life. The medical device sector also benefits from this technology, as it allows for the efficient production of sterile containers and surgical tools with precise joins.
Conclusion
The automatic high frequency welder represents a significant advancement in welding technology that offers numerous benefits for modern manufacturing. Its ability to produce high-quality, consistent welds at impressive speeds makes it an invaluable asset in various industries. As businesses continue to strive for efficiency while maintaining product integrity, the adoption of automatic high frequency welders will likely become even more prevalent, helping companies meet the ever-increasing demands of the market. Embracing such advanced technologies not only enhances production capabilities but also ensures that industries can adapt to evolving customer needs and regulatory standards.Tube Mill Spare Parts Supplier