[Precision-control All-in-one Welding Equipment]Revolutionizing Metal Fabrication: The Advantages of Precision-Control All-in-One Welding Equipment for Modern Industry Needs
In the fast-paced world of metal fabrication, efficiency and precision are paramount. As industries evolve and the demand for high-quality welds increases, manufacturers are continually seeking out advanced solutions that not only enhance productivity but also ensure superior outcomes. One such innovation making waves in the welding sector is the precision-control all-in-one welding equipment. This state-of-the-art technology offers an unprecedented blend of versatility and precision, meeting the diverse needs of modern welding applications.
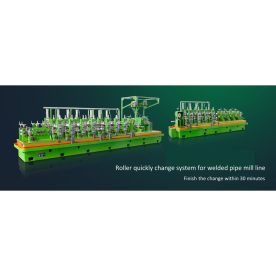
Revolutionizing Metal Fabrication: The Advantages of Precision-Control All-in-One Welding Equipment for Modern Industry Needs
What is Precision-Control All-in-One Welding Equipment?
Precision-control all-in-one welding equipment refers to machines that consolidate multiple welding processes into a single, streamlined device. Typically, these units allow users to perform various welding techniques, such as MIG, TIG, and stick welding, all from one machine. The integration of precision control technology enables users to adjust settings in real-time, ensuring that welds are consistent and meet specific engineering requirements. This flexibility is particularly beneficial in industries where different welding methods are required for different tasks.

Revolutionizing Metal Fabrication: The Advantages of Precision-Control All-in-One Welding Equipment for Modern Industry Needs
Key Features of Precision-Control All-in-One Welding Equipment
1. **Advanced Control Systems**: These machines are equipped with digital controls that allow for precise adjustments to voltage, speed, and feed rates. Advanced user interfaces and programmable settings enable users to easily switch between different welding processes without sacrificing quality.
2. **Portability**: The compact design of all-in-one welding equipment allows for easy transportation. This portability is especially advantageous for fieldwork and on-site repairs, where space may be limited, and mobility is crucial.
3. **Multi-Functionality**: Instead of investing in multiple machines, a precision-control all-in-one welder consolidates the need for several devices into a single investment. This not only saves money but also minimizes the footprint in workshops.
4. **Improved Weld Quality**: With precise settings, the quality of welds is improved significantly. Users can achieve cleaner, stronger welds with reduced splatter and minimal post-weld cleanup.

Revolutionizing Metal Fabrication: The Advantages of Precision-Control All-in-One Welding Equipment for Modern Industry Needs
5. **User-Friendly Interfaces**: Modern all-in-one welding machines come with intuitive controls that simplify the welding process, making them accessible for both novice and experienced welders.
The Benefits of Using Precision-Control All-in-One Welding Equipment
1. **Cost-Efficiency**: By integrating multiple functions into one machine, businesses can reduce initial capital expenditures and save on maintenance costs moving forward. The versatility of these machines also means that they can handle various tasks within a manufacturing process, further cutting down operational costs.
2. **Increased Productivity**: The ability to switch between different welding processes quickly can drastically reduce downtime. Whether it’s switching from MIG to TIG welding or adjusting settings for different materials, reduced setup time allows for faster project completion.
3. **Enhanced Welding Skills**: For companies that employ less experienced welders, precision-control equipment can facilitate skill development. The adjustable settings enable users to practice and hone their skills without the need for multiple machines or advanced setups.
4. **Consistency and Quality Assurance**: With precision controls, users can reproduce the same weld quality consistently across numerous projects. This capability is vital in industries where specifications are strict, such as automotive and aerospace.
5. **Reduced Waste and Rework**: The precise nature of the welding performed with these machines minimizes errors, thereby reducing material waste. The high-quality welds produced often require less rework, which means that businesses can operate more efficiently.
Conclusion
Precision-control all-in-one welding equipment is transforming the way industries approach welding tasks. By offering a blend of versatility, efficiency, and quality, these machines provide significant advantages to fabricators looking to keep pace with modern demands. As technology continues to advance, companies that invest in this type of equipment are better positioned for success in an increasingly competitive market. The future of welding is undoubtedly moving toward more integrated and precise solutions, making these all-in-one machines a wise choice for any welding operation.Customized induction heating equipment