[High frequency welder machine]Understanding High Frequency Welder Machines: Applications, Benefits, and Key Considerations for Your Manufacturing Needs
In today’s manufacturing landscape, the demand for efficient, reliable, and high-quality welding processes is ever-increasing. One innovation that has significantly transformed welding technology is the high frequency welder machine. These advanced machines offer a range of advantages over traditional welding methods, making them ideal for various applications across different industries. This article aims to provide an in-depth understanding of high frequency welding technology, its applications, benefits, and considerations for your manufacturing needs.
What is a High Frequency Welder Machine?
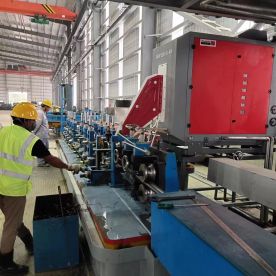
Understanding High Frequency Welder Machines: Applications, Benefits, and Key Considerations for Your Manufacturing Needs
A high frequency welder machine utilizes high-frequency electrical currents to create heat, which in turn fuses materials together. The process involves generating electromagnetic waves that induce a rapid increase in temperature at the interface of the materials being welded. This technique is particularly effective for welding thin materials or thermoplastic components. Unlike conventional welding methods, which can produce a significant amount of heat and result in more considerable distortion of the workpieces, high frequency welding operates at much lower temperatures, leading to a more controlled and precise welding process.
Applications of High Frequency Welder Machines
High frequency welders are widely used in several industries due to their versatility and effectiveness. Here are some of the key applications:
1. **Plastic Fabrication**: One of the most common uses of high frequency welders is in the plastic industry. These machines are ideal for welding vinyl, PVC, and other thermoplastic materials to create items such as inflatable products, medical bags, and packaging films.
2. **Automotive Industry**: High frequency welding is employed for producing critical components like fuel tanks, air ducts, and protective covers. The ability to weld thin and complex shapes efficiently makes this process an attractive option for automotive manufacturers.
3. **Textile Industry**: High frequency welders are used in the production of waterproof and airtight textiles, commonly found in outdoor gear, tents, and medical applications. The precision of this welding method ensures the durability and quality required for these products.
4. **Electrical and Electronic Components**: The electronics industry benefits from high frequency welding for assembling components like transformers and capacitors. The process guarantees a strong bond that is essential for the reliability of electronic devices.
5. **Aerospace and Defense**: Due to its high precision and reliability, high frequency welding is also utilized in the aerospace sector for producing lightweight and durable components.
Benefits of High Frequency Welder Machines
Investing in high frequency welder machines offers several advantages, including:
1. **Precision**: High frequency welding allows for tight control over the welding process, leading to consistent quality and less distortion of materials.
2. **Speed**: The rapid welding process facilitated by these machines significantly reduces production time, enhancing overall productivity in manufacturing operations.
3. **Cost-Effective**: Although the initial investment might be higher compared to traditional welding equipment, the long-term savings in terms of material efficiency, reduced waste, and faster production cycles can make high frequency welders a cost-effective solution.
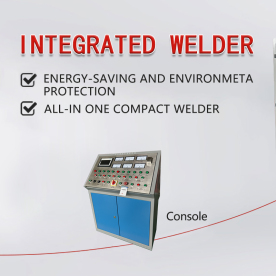
Understanding High Frequency Welder Machines: Applications, Benefits, and Key Considerations for Your Manufacturing Needs
4. **Versatility**: High frequency welders can accommodate a wide range of materials, making them suitable for various applications across industries. The ability to weld different thicknesses and shapes adds to their appeal.
5. **Reduced Heat Affected Zone (HAZ)**: The localized heating minimizes the heat-affected zone, reducing the risk of warping and degradation of the material’s properties.
Key Considerations for Choosing a High Frequency Welder Machine
When selecting a high frequency welder machine for your manufacturing needs, it is crucial to consider the following factors:
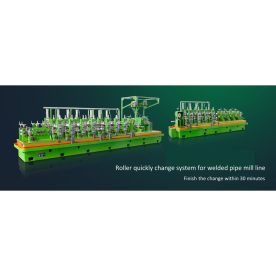
Understanding High Frequency Welder Machines: Applications, Benefits, and Key Considerations for Your Manufacturing Needs
1. **Material Compatibility**: Ensure that the machine is compatible with the types of materials you plan to weld. Different machines may have specifications tailored for specific materials.
2. **Power Requirements**: Assess the power capabilities of the welder, as higher power often translates to faster and more effective welding processes.
3. **Automation and Control Features**: Evaluate the level of automation and control offered by the machine. Advanced features can enhance precision and reduce the need for manual intervention.
4. **Maintenance and Support**: Consider the availability of technical support and maintenance services for the machine. Reliable service can minimize downtime and enhance productivity.
5. **Cost**: While it’s important to find a machine within your budget, make sure to balance cost with the features and capabilities that meet your specific welding needs.
Conclusion
High frequency welder machines represent a significant advancement in welding technology, enabling manufacturers to achieve high-quality, efficient, and versatile welding solutions. By understanding the various applications, benefits, and considerations of high frequency welders, businesses can better navigate their manufacturing needs and gain a competitive edge in their respective industries. Investing in technology that enhances precision and productivity will undoubtedly lead to improved outcomes in the long run.Tailor-Made Spare Parts for Tube Mills