[Advanced Tube making machinery]Exploring the Innovative Advancements in Advanced Tube Making Machinery: Revolutionizing Industries with Precision and Efficiency
****
In the realm of manufacturing, the production of high-quality tubes plays a crucial role in various industries including aerospace, automotive, construction, and energy. With the constant demand for efficiency and precision, the evolution of technology has led to the development of Advanced Tube Making Machinery. This sophisticated equipment not only enhances the quality of tubes produced but also significantly optimizes the manufacturing process. This article delves deep into the intricacies of advanced tube making machinery, its components, functions, and the advantages it brings to modern manufacturing.
The Evolution of Tube Making Machinery
Historically, tube production was a labor-intensive process dominated by manual operations and basic machinery. As industries progressed, so did the need for more efficient and effective production methods. The introduction of Advanced Tube Making Machinery marks a pivotal shift in how tubes are fabricated, allowing manufacturers to meet the increasing demands for high-quality products at a lower cost and faster production rates.
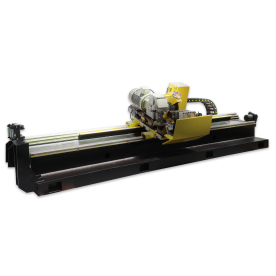
Exploring the Innovative Advancements in Advanced Tube Making Machinery: Revolutionizing Industries with Precision and Efficiency
Key Components of Advanced Tube Making Machinery
Advanced tube making machinery encompasses a variety of intricate components working in unison to ensure optimal performance. Some of the essential components include:
1. **Forming Units**: The heart of tube production, these units shape the raw materials into precise forms. Depending on the type of tube being produced, the forming process can include techniques such as roll forming, stretch forming, or hydroforming.
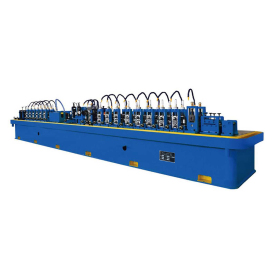
Exploring the Innovative Advancements in Advanced Tube Making Machinery: Revolutionizing Industries with Precision and Efficiency
2. **Welding Systems**: After forming, the edges of the tubes must be joined together, which is typically achieved through advanced welding technologies. Laser welding, for example, provides exceptional precision and strength, ensuring the product meets stringent industry standards.
3. **Cutting and Trimming Equipment**: Once the tubes are formed and welded, they are cut to the desired lengths. Advanced machinery features automated cutting systems that ensure accuracy and reduce waste, offering a significant advantage over traditional methods.
4. **Inspection and Testing Units**: Quality control is paramount in tube manufacturing. Advanced machinery often includes integrated inspection systems that utilize technologies like ultrasonic testing, eddy current testing, and visual inspection to ensure that each tube meets the necessary specifications.
5. **Control Systems**: High-tech control systems manage the entire production process, allowing operators to monitor and adjust parameters in real-time. This enhances the flexibility of the machinery and minimizes downtime due to inefficiencies or malfunctions.
Benefits of Advanced Tube Making Machinery
The integration of advanced technology into tube making processes offers numerous benefits for manufacturers:
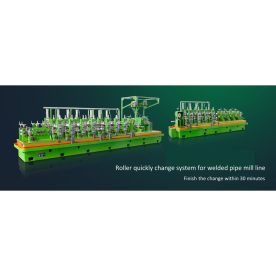
Exploring the Innovative Advancements in Advanced Tube Making Machinery: Revolutionizing Industries with Precision and Efficiency
– **Increased Efficiency**: Advanced machinery automates many aspects of tube production, which reduces cycle times and allows manufacturers to produce higher quantities of tubes within shorter periods.
– **Enhanced Quality**: With precise controls and advanced inspection technologies, manufacturers can achieve superior quality in their finished products. This is particularly essential in industries where safety and reliability are paramount.
– **Cost Reduction**: Although the initial investment in advanced machinery may be significant, the long-term savings in labor costs, material waste, and increased production output often outweigh the expenses.
– **Flexibility**: Modern tube making machinery can often be adjusted to produce a wide variety of tube sizes and materials without requiring extensive retooling, making it easier for manufacturers to respond to changing market demands.
– **Sustainability**: Advanced equipment often incorporates energy-efficient technologies and practices, helping manufacturers reduce their carbon footprint and contribute to more sustainable production processes.
Future Outlook
As the manufacturing landscape evolves, the reliance on Advanced Tube Making Machinery will only continue to grow. Innovations in artificial intelligence, automation, and material science are poised to further revolutionize tube production, leading to even greater efficiencies and new applications.
In conclusion, Advanced Tube Making Machinery represents a significant leap in manufacturing technology, providing essential solutions to meet contemporary market demands. By integrating advanced machinery into their production processes, manufacturers can ensure they remain competitive in an increasingly demanding environment while delivering high-quality products to their customers. Such advancements will undoubtedly shape the future of tube manufacturing and its applications across various industries.Tube making machine for industrial applications