[Cold Cutting Saw Machine for Metal]Unlocking Precision and Efficiency in Metal Fabrication with Cold Cutting Saw Machines: A Comprehensive Guide
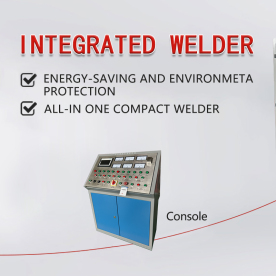
Unlocking Precision and Efficiency in Metal Fabrication with Cold Cutting Saw Machines: A Comprehensive Guide
****
In the metalworking industry, precision and efficiency are paramount. As manufacturers strive to enhance productivity while maintaining the highest standards of quality, Cold Cutting Saw Machines for Metal have emerged as an indispensable tool. These machines not only provide superior cutting capabilities but also ensure minimal material wastage, making them a vital asset for workshops and factories alike. This article delves into the intricacies of cold cutting saw machines, exploring their advantages, applications, and best practices for optimal use.
Understanding Cold Cutting Saw Machines
Cold cutting saw machines are specialized equipment designed to sever metal with a blade that operates at lower temperatures compared to traditional cutting methods such as band saws or abrasive saws. Powered by electric motors, these machines typically use carbide-tipped blades that are engineered to handle various metal types, including aluminum, stainless steel, and other ferrous and non-ferrous materials.
One of the key characteristics of cold cutting saws is that they minimize heat generation during the cutting process. This is critical in preventing thermal distortion of the material, which can compromise the integrity of the metal and result in costly rework or waste. Additionally, the quality of the finished cut is significantly improved, with smooth edges and precise dimensions, making it easier to prepare parts for subsequent machining or assembly.
Advantages of Cold Cutting Saw Machines for Metal
The benefits of using cold cutting saw machines in metal fabrication can be categorized into several key areas:
1. **Precision Cutting**: Cold cutting saws deliver highly accurate results, making them suitable for tight tolerances in manufacturing. The ability to maintain consistent dimensions throughout a production run helps manufacturers achieve their quality standards and reduces the likelihood of errors.
2. **Lower Heat Generation**: The reduced heat during cutting means that there is less risk of metallurgical changes in the material. This quality is essential for maintaining the properties of specific alloys and ensuring that the finished products have the desired strength and durability.
3. **Improved Surface Finish**: The operation of cold cutting saw machines typically results in a superior surface finish compared to traditional saws. This is beneficial in reducing the amount of post-processing, such as grinding or sanding, ultimately saving time and costs.
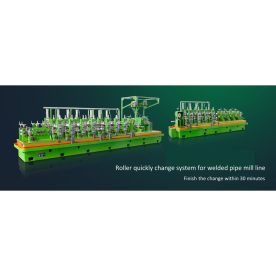
Unlocking Precision and Efficiency in Metal Fabrication with Cold Cutting Saw Machines: A Comprehensive Guide
4. **Enhanced Efficiency**: With faster cutting speeds and shorter cycle times, cold cutting saw machines enable manufacturers to elevate their production rates. The efficiency gained from these machines can lead to quicker turnaround times, allowing businesses to meet customer demand more effectively.
5. **Versatility**: These machines are capable of cutting a wide range of materials, from soft metals to harder alloys, making them adaptable to a variety of applications. This versatility allows workshops to streamline their equipment and reduce the need for multiple cutting tools.
Applications in the Metalworking Industry
Cold cutting saw machines find applications across various sectors of the metalworking industry, including:
– **Manufacturing**: In manufacturing plants, cold cutting saws are employed for bulk production of components requiring precise cuts, such as brackets, fittings, and frames. – **Fabrication Shops**: Metal fabricators use these machines to create customized parts and assemblies, often for a diverse range of industries such as automotive, aerospace, and construction.
– **Metal Recycling**: Cold cutting saws facilitate the processing of scrap metal, allowing recyclers to efficiently cut materials for sorting and recycling.
Best Practices for Operating Cold Cutting Saw Machines
To ensure optimal performance and longevity of cold cutting saw machines, users should follow several best practices:

Unlocking Precision and Efficiency in Metal Fabrication with Cold Cutting Saw Machines: A Comprehensive Guide
1. **Regular Maintenance**: Scheduled maintenance is essential for keeping the machine in top working condition. This includes checking the alignment of the saw blade, lubricating moving parts, and inspecting the cutting tools for wear.
2. **Proper Blade Selection**: Using the correct blade type and size for the material being cut is critical. Different materials require different blade configurations, and selecting the right one ensures efficiency and precision.
3. **Optimal Speed and Feed Rates**: Adjusting the cutting speed and feed rate according to the material can greatly influence the quality of the cut. It is essential for operators to refer to manufacturer guidelines and make adjustments based on their specific work environments.
4. **Safety Precautions**: Operators should always wear appropriate safety gear, including goggles and protective gloves, when operating cold cutting saw machines. Additionally, ensuring a clean work environment and proper training for machine operators can mitigate the risks associated with metal cutting.
Conclusion
Cold Cutting Saw Machines for Metal represent a significant advancement in the metalworking industry, providing manufacturers with the capability to achieve precision cuts with enhanced efficiency. By understanding their advantages, applications, and best practices, businesses can leverage these machines to improve their processes, reduce waste, and ultimately deliver higher quality products to their customers. As technology continues to progress, cold cutting saws will undoubtedly play an even larger role in the future of metal fabrication.Cold Cutting Saw Machine Replacement Parts