[Automatic induction heating equipment]Exploring the Advantages and Applications of Automatic Induction Heating Equipment for Modern Industrial Processes
****
In today’s fast-paced industrial landscape, efficiency and precision are paramount for maintaining competitive advantages. Among the technologies that have drastically transformed manufacturing processes, automatic induction heating equipment stands out as a remarkable solution. This equipment utilizes electromagnetic induction to heat conductive materials, making it an essential component across various industries, including automotive, aerospace, metalworking, and more. This article will delve into the mechanisms of automatic induction heating, its numerous applications, and the myriad benefits it offers to manufacturers today.
What is Automatic Induction Heating Equipment?
Automatic induction heating equipment operates on the principle of electromagnetic induction. This technology involves generating an alternating magnetic field that induces electric currents (also known as eddy currents) within conductive materials. As these currents flow through the material, they produce heat due to the material’s inherent resistance. The result is an efficient and controlled heating process that can be utilized for various applications, including hardening, melting, welding, and brazing.
One of the key features of automatic induction heating equipment is its ability to precisely control the heating process. The temperature can be adjusted to meet specific requirements, ensuring uniform heating and reducing the risk of over or under-heating. Such automation not only enhances product quality but also minimizes the need for manual intervention, leading to increased efficiency and reduced labor costs.
Applications of Automatic Induction Heating Equipment
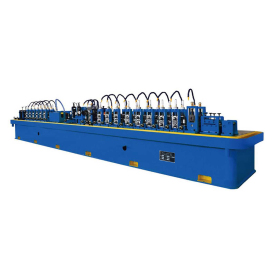
Exploring the Advantages and Applications of Automatic Induction Heating Equipment for Modern Industrial Processes
1. **Metal Hardening and Annealing**: One of the primary uses of induction heating is in the heat treatment of metal components. The equipment can rapidly heat parts to specified temperatures, allowing for processes like quenching and tempering. This is especially valuable in industries that require enhanced strength and durability in their products, such as automotive and aerospace manufacturing.
2. **Brazing and Soldering**: In applications where metals need to be joined without melting the base materials, induction heating equipment is invaluable. It can produce localized heating, allowing precise control over the solder or braze joint without affecting the surrounding areas. This level of precision is crucial in electronics and plumbing applications where heat-sensitive components are involved.
3. **Melting Metal**: For foundries and metal recyclers, automatic induction heating provides a highly effective method for melting metals. The ability to heat materials evenly and quickly facilitates efficient melting processes, reducing energy consumption and improving turnaround times.
4. **Thermal Forming**: Induction heating can be used in the thermal forming of plastics and other non-metal materials. By heating the material uniformly, manufacturers can shape complex designs with accuracy and efficiency.
5. **Preheating for Welding**: Before welding, preheating components can be essential to avoid thermal shock and improve weld quality. Induction heating equipment can quickly bring parts to the desired temperature, enhancing the overall welding process.
Advantages of Automatic Induction Heating Equipment
1. **Energy Efficiency**: Automatic induction heating is highly efficient, with minimal energy loss during the heating process. The direct heating of the workpiece minimizes the need for additional heating methods, reducing overall energy consumption and costs.
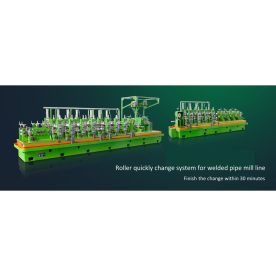
Exploring the Advantages and Applications of Automatic Induction Heating Equipment for Modern Industrial Processes
2. **Speed**: The ability to quickly heat materials significantly reduces cycle times. This speed allows manufacturers to increase production rates and meet tight deadlines.

Exploring the Advantages and Applications of Automatic Induction Heating Equipment for Modern Industrial Processes
3. **Precision and Control**: Automatic induction heating provides precise control over the heating process, allowing for accurate temperature settings and uniform heating. This is particularly important in industries where material properties are critical, such as aerospace and automotive manufacturing.
4. **Reduced Oxidation and Contamination**: Traditional heating methods often result in oxidation and other surface contamination issues. Induction heating minimizes these risks due to its localized heating approach, preserving the integrity of the heated materials.
5. **Automation and Labor Savings**: With advancements in technology, automatic induction heating equipment can be integrated with automation systems, reducing the need for manual handling and increasing overall operational efficiency.
Conclusion
Automatic induction heating equipment has emerged as a revolutionary tool in modern industrial applications, offering enhanced efficiency, precision, and versatility. By understanding the principles, applications, and advantages of this technology, manufacturers can leverage induction heating to optimize their operations and produce high-quality products. As industries continue to evolve and demand more innovative solutions, automatic induction heating equipment will remain at the forefront of technological advancement in the manufacturing sector.Industrial induction heating equipment