[Advanced induction heating equipment technology]Revolutionizing Manufacturing Processes: The Impact of Advanced Induction Heating Equipment Technology on Efficiency and Precision
****
In today’s rapidly evolving industrial landscape, the demand for precision-engineered components has never been greater. Manufacturers are constantly seeking innovative technologies that can enhance productivity while maintaining high quality. One such groundbreaking technology is advanced induction heating equipment. This sophisticated method is transforming the way heat is applied in industrial processes, leading to significant improvements in efficiency, accuracy, and overall output.
Induction heating is a process that uses electromagnetic induction to heat electrically conductive materials. Unlike traditional heating methods that rely on external heat sources, induction heating induces heat directly within the material itself. This leads to a range of benefits, including faster heating times, reduced energy consumption, and more uniform temperature distribution. As manufacturing technologies advance, the capabilities and applications of induction heating equipment have expanded, offering new opportunities across various industries.
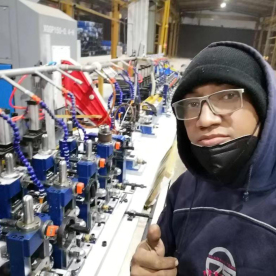
Revolutionizing Manufacturing Processes: The Impact of Advanced Induction Heating Equipment Technology on Efficiency and Precision
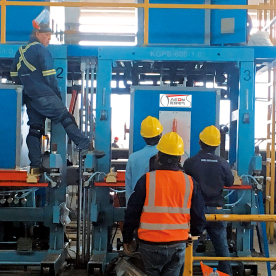
Revolutionizing Manufacturing Processes: The Impact of Advanced Induction Heating Equipment Technology on Efficiency and Precision
One of the primary advantages of advanced induction heating equipment technology is its remarkable efficiency. Traditional heating methods, such as convection or resistance heating, often waste a substantial amount of energy. In contrast, induction heating can achieve efficiencies of over 90%. This is particularly important in an era where industries are under constant pressure to reduce operating costs and minimize their carbon footprints. By utilizing advanced induction heating systems, manufacturers can not only enjoy lower energy bills but also contribute to sustainability efforts.
Precision is another crucial aspect where advanced induction heating equipment shines. The ability to control heating times and temperatures with pinpoint accuracy allows manufacturers to achieve consistent results, which is essential in high-stakes applications such as aerospace, automotive, and medical device manufacturing. In these sectors, even the slightest variation in temperature can lead to product defects or failures. With sophisticated induction heating technology, manufacturers can ensure that each component meets stringent quality standards, leading to increased reliability and customer satisfaction.
Moreover, the versatility of advanced induction heating systems enables their application in a wide range of processes, including hardening, brazing, soldering, melting, and more. For example, in the metalworking industry, induction heating is used to harden the surface of parts without affecting the integrity of the underlying material. This is particularly valuable for components that require high wear resistance while maintaining toughness. The ability to achieve localized heating without affecting the surrounding areas is a game-changer for many manufacturing processes.
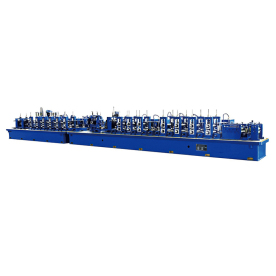
Revolutionizing Manufacturing Processes: The Impact of Advanced Induction Heating Equipment Technology on Efficiency and Precision
The realm of induction heating technology has seen significant advancements in recent years, driven by innovations in digital controls and sensor technology. Modern induction heating equipment often comes equipped with sophisticated software that provides real-time monitoring and analytics. This enables manufacturers to optimize heating cycles, track energy consumption, and foresee maintenance needs, resulting in minimized downtime and enhanced operational effectiveness.
The integration of Industry 4.0 principles with advanced induction heating technology is another exciting development. Manufacturers are increasingly using the Internet of Things (IoT) to connect their induction heating equipment to centralized systems that allow for remote monitoring and control. This connectivity not only enhances predictive maintenance capabilities but also enables manufacturers to adjust parameters on-the-fly to optimize performance. As a result, businesses can adapt more quickly to changing production requirements and maintain a competitive edge in a fast-paced market.
Additionally, advanced induction heating technology lends itself well to automation, further enhancing operational efficiency. Automated induction heating systems can be programmed to follow specific heating profiles for different materials or components, reducing the need for human intervention. This is particularly beneficial in settings where bulk production is required, as it ensures consistency and reduces labor costs.
In summary, advanced induction heating equipment technology is reshaping the manufacturing landscape by delivering enhanced efficiency, precision, and versatility. As industries continue to demand higher quality standards and more sustainable practices, the adoption of induction heating technology is poised to increase. For manufacturers looking to innovate and stay ahead of the curve, investing in advanced induction heating technology is not just a strategic choice; it is essential for future success. As we look ahead, it is clear that this technology will play a pivotal role in defining the next generation of manufacturing excellence.Cost-Effective HSS Blade Solution