[IF pipe seam annealing machine ]Revolutionizing Steel Manufacturing: The Importance of IF Pipe Seam Annealing Machines in Enhancing Weld Quality and Efficiency
In the ever-evolving landscape of modern manufacturing, the demand for high-quality steel pipes continues to rise. One of the critical processes in the production of steel pipes is seam annealing, a method designed to enhance the mechanical properties of welded seams, thereby ensuring the durability and performance of the product. Specifically, the induction furnace (IF) pipe seam annealing machine stands out as a beacon of innovation in this domain, offering unprecedented advantages that significantly improve both manufacturing processes and end-product quality.
What is IF Pipe Seam Annealing?
The IF pipe seam annealing process involves the controlled heating of welded steel pipes using induction heating technology. This method focuses on selectively heating the seam area of welded pipes, allowing for precise temperature control and rapid heat application. The primary objective is to relieve internal stresses generated during the welding process, promote microstructural changes, and enhance the overall mechanical properties, including strength, ductility, and toughness of the pipe.
The Technology Behind IF Pipe Seam Annealing Machines
Induction heating is based on the principle of electromagnetic induction, where an alternating magnetic field induces an electric current within the material. This current generates heat due to the electrical resistance of the material. For the IF pipe seam annealing machine, specialized coils are utilized to create an electromagnetic field that uniformly heats the weld seam without affecting the surrounding areas of the pipe. This targeted heating results in minimal distortion and allows for very efficient heating cycles, significantly reducing processing time.
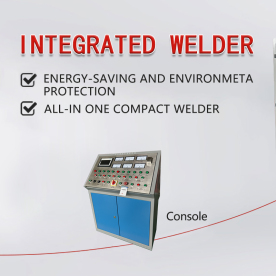
Revolutionizing Steel Manufacturing: The Importance of IF Pipe Seam Annealing Machines in Enhancing Weld Quality and Efficiency
Benefits of Using IF Pipe Seam Annealing Machines
1. **Enhanced Weld Quality**: The primary advantage of using IF pipe seam annealing machines is the improvement in weld quality. By properly annealing the weld seam, the machine effectively alleviates residual stresses, reduces hardness, and eliminates any potential for cracking and other defects.
2. **Increased Productivity**: The efficiency of induction heating allows for faster cycle times compared to traditional methods. As a result, manufacturers can produce higher volumes of high-quality products in shorter periods. This increase in productivity translates into significant cost savings and improved competitiveness in the market.
3. **Energy Efficiency**: IF pipe seam annealing machines consume less energy than traditional furnace systems. The induction heating method is inherently more efficient, as it directly heats the workpiece without the need for a large external heat source. This leads to lower operational costs and a reduced carbon footprint, aligning with modern sustainability goals in manufacturing.
4. **Versatile Applications**: These machines are adaptable, capable of handling various pipe sizes and materials, including carbon steel, alloy steel, and stainless steel. This versatility makes IF pipe seam annealing machines a valuable asset in various industries such as oil and gas, construction, and automotive.
5. **Improved Product Consistency**: The precise control offered by IF pipe seam annealing machines results in greater consistency in the quality of the finished product. Uniform heating contributes to homogeneity in the material’s properties, which is critical in applications where performance and safety are paramount.
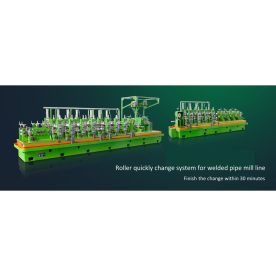
Revolutionizing Steel Manufacturing: The Importance of IF Pipe Seam Annealing Machines in Enhancing Weld Quality and Efficiency
6. **Reduced Operational Risks**: The advancements in automation and control technologies integrated into modern IF pipe seam annealing machines reduce the potential for human error. Operators can monitor the process through sophisticated control systems, ensuring that optimal conditions are maintained throughout the annealing cycle.

Revolutionizing Steel Manufacturing: The Importance of IF Pipe Seam Annealing Machines in Enhancing Weld Quality and Efficiency
Conclusion
As the industrial sector continues to push boundaries in terms of efficiency and quality, the role of technology in enhancing manufacturing processes cannot be overstated. The IF pipe seam annealing machine exemplifies this technological advancement, providing manufacturers with a powerful tool to improve the quality and performance of welded steel pipes. By offering notable benefits such as enhanced weld quality, increased productivity, energy efficiency, and versatility, these machines pave the way for achieving higher standards in steel pipe production. As industries continue to evolve, the adoption of innovative solutions like the IF pipe seam annealing machine will be critical in meeting the demands of the future while upholding the quality and safety of essential products.High frequency welder for metal