[High-efficiency All-in-one Welding System]Exploring the Benefits and Advancements of High-Efficiency All-in-One Welding Systems for Modern Industry Applications
In recent years, the welding industry has witnessed significant technological advancements that have transformed traditional practices into highly efficient and versatile solutions. Among these innovations, the High-Efficiency All-in-One Welding System has emerged as a game changer, delivering exceptional performance, flexibility, and cost savings. This article will delve into the mechanics of these systems, their benefits, and their implications for various industry applications.
Understanding High-Efficiency All-in-One Welding Systems
At its core, a High-Efficiency All-in-One Welding System integrates multiple welding processes and functions into a single machine. This could encompass MIG (Metal Inert Gas), TIG (Tungsten Inert Gas), stick welding, and even plasma cutting in one compact unit. These systems are designed to cater to a diverse range of materials, such as steel, aluminum, and stainless steel, making them suitable for various industrial applications, including automotive, aerospace, construction, and manufacturing.
One of the defining characteristics of these systems is their efficiency. High-efficiency systems utilize advanced technologies such as inverter technology, which reduces energy consumption while providing a stable arc, improving weld quality. This translates to less downtime and higher productivity, essential components in today’s fast-paced manufacturing environments.
Versatility in Application
The versatility of High-Efficiency All-in-One Welding Systems is one of their most attractive features. Traditionally, welders had to use separate machines for different types of welding processes, which not only consumed more space but also required more time to switch between setups. With an all-in-one system, operators can easily switch from one welding process to another without complex recalibrations or equipment changes.
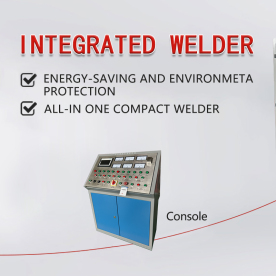
Exploring the Benefits and Advancements of High-Efficiency All-in-One Welding Systems for Modern Industry Applications
This adaptability makes these systems ideal for job shops and fabrication facilities that handle a variety of projects, from custom machinery fabrication to complex assembly work. Additionally, with the option to perform multiple welding types in one machine, businesses can respond quickly to customer requirements, ultimately fostering stronger relationships and improving service delivery.
Cost-Effectiveness
Investing in a High-Efficiency All-in-One Welding System can yield significant cost savings for companies. First and foremost, the initial investment in one multifunctional machine is generally lower than purchasing multiple standalone units. This streamlined approach can reduce maintenance costs, as managing one piece of equipment is typically simpler than coordinating multiple machines with individual maintenance schedules.
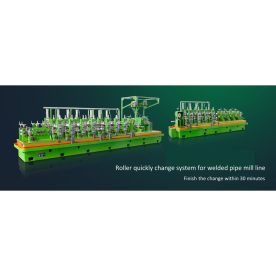
Exploring the Benefits and Advancements of High-Efficiency All-in-One Welding Systems for Modern Industry Applications
Furthermore, the energy efficiency of these systems contributes to lower operational costs. With inverter technology, they consume less power while maintaining optimal performance, which is a critical consideration, especially in large-scale operations where energy bills can quickly add up.
Enhanced Weld Quality and Consistency
One of the most vital aspects of welding is the quality and consistency of the welds produced. High-Efficiency All-in-One Welding Systems are equipped with advanced features such as microprocessor-controlled settings and programmable parameters that enhance weld quality. These systems can adjust power output and feed rates in real time, resulting in a more uniform weld bead and reducing the occurrence of defects.

Exploring the Benefits and Advancements of High-Efficiency All-in-One Welding Systems for Modern Industry Applications
Additionally, the automation capabilities in modern welding systems facilitate better quality control. By employing automated processes and monitoring technologies, operators can minimize human error, ensuring that every weld meets the required specifications. This reliability becomes crucial in industries where safety and quality are paramount, such as in the aerospace and automotive sectors.
Conclusion
In summary, High-Efficiency All-in-One Welding Systems represent a remarkable evolution in welding technology. Their blend of versatility, cost-effectiveness, and enhanced weld quality positions them as a preferred choice across various industries. As businesses strive to improve their operational efficiencies and respond to the dynamic market demands, these systems stand out as a crucial investment for the future. Companies that adopt these advanced systems will not only benefit from immediate improvements in productivity and cost savings but also gain a competitive edge in an increasingly demanding marketplace. As technology continues to evolve, we can expect these all-in-one systems to become even more integral to the fabric of modern industry applications.Cost-Effective Spare Parts for Cold Cutting Saws