[Tube Mill Spare Parts Supplier]Troubleshooting Common Issues with Tube Mill Spare Parts Supplier: Expert Tips and Solutions
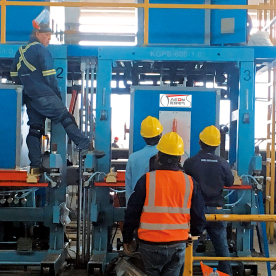
Troubleshooting Common Issues with Tube Mill Spare Parts Supplier: Expert Tips and Solutions
When it comes to operating a tube mill, having a reliable spare parts supplier is crucial. But sometimes, even the best suppliers can encounter issues that may impact production efficiency and quality. In this article, we will discuss some common problems that tube mill spare parts suppliers may face and provide expert tips and solutions to help resolve them.
One of the most common issues that tube mill spare parts suppliers encounter is delays in delivery. This can be caused by various factors, such as inventory shortages, production issues, or unforeseen circumstances. To address this problem, it is essential for suppliers to maintain regular communication with their customers and provide accurate lead times for each order. By keeping customers informed about the status of their orders, suppliers can manage expectations and minimize dissatisfaction.
Another common issue that suppliers may face is quality control problems. This can range from receiving defective parts from manufacturers to shipping incorrect items to customers. To avoid quality control issues, suppliers should establish strict standards for incoming and outgoing inspections. By thoroughly inspecting all parts before shipping them to customers, suppliers can ensure that only high-quality products are delivered. Additionally, suppliers should work closely with their manufacturing partners to address any quality issues promptly and prevent them from recurring in the future.
Inconsistent pricing is another challenge that tube mill spare parts suppliers may encounter. Pricing discrepancies can result from fluctuating material costs, currency exchange rates, or miscommunication between sales and finance teams. To prevent pricing issues, suppliers should implement a robust pricing strategy that accounts for market fluctuations and ensures consistency across all customer transactions. By regularly reviewing and updating pricing models, suppliers can avoid misunderstandings with customers and maintain profitability.
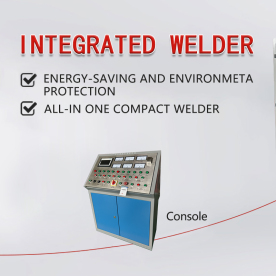
Troubleshooting Common Issues with Tube Mill Spare Parts Supplier: Expert Tips and Solutions
Furthermore, inventory management can be a significant obstacle for tube mill spare parts suppliers. Maintaining an optimal level of inventory is essential to meet customer demand while minimizing carrying costs. Suppliers should implement advanced inventory management tools and techniques, such as just-in-time ordering and demand forecasting, to optimize their inventory levels. By actively managing inventory, suppliers can improve order fulfillment rates, reduce lead times, and increase customer satisfaction.
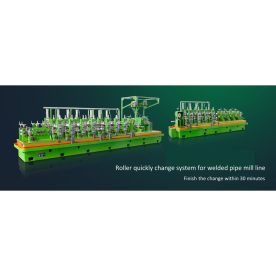
Troubleshooting Common Issues with Tube Mill Spare Parts Supplier: Expert Tips and Solutions
Lastly, customer service is vital for tube mill spare parts suppliers to build long-term relationships with their clients. Excellent customer service involves promptly addressing customer inquiries, providing accurate information, and resolving any issues that may arise. By cultivating a customer-centric culture within their organization, suppliers can enhance customer loyalty and attract new business opportunities. Additionally, suppliers should actively seek feedback from customers to identify areas for improvement and make necessary adjustments to enhance their service quality continually.
In conclusion, tube mill spare parts suppliers may encounter various challenges in their operations. By implementing effective strategies for addressing common issues, such as delivery delays, quality control problems, inconsistent pricing, inventory management, and customer service, suppliers can enhance their competitiveness and drive sustainable growth. By focusing on continuous improvement and meeting customer needs, tube mill spare parts suppliers can thrive in a dynamic and competitive marketplace.All-in-one High Frequency Welder for Metal Processing