[Roller for tube mill]Exploring the Essential Role of Rollers in Tube Mill Operations: Enhancing Efficiency, Quality, and Productivity
In the world of metal fabrication and manufacturing, the tube mill stands out as a vital machine used to produce a variety of tubular products used in construction, automotive, and aerospace industries. At the heart of tube mill operations lies an essential component known as the roller. This article delves into the critical role that rollers play in the efficiency, quality, and productivity of tube mills, exploring their design, types, functions, and the innovations driving their evolution.
Understanding the Tube Mill Process
A tube mill operates by bending and welding flat sheets of metal into tubular shapes. This process involves several stages, including decoiling, shaping, welding, and finishing. Each step is crucial, but it is the roller system that significantly influences the overall performance of the tube mill. Rollers guide the metal sheets along the forming stations, ensuring consistent shapes and weld quality.
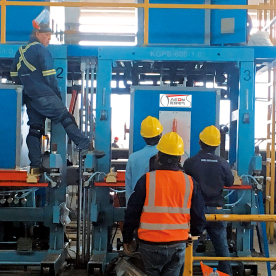
Exploring the Essential Role of Rollers in Tube Mill Operations: Enhancing Efficiency, Quality, and Productivity
Types of Rollers in Tube Mills
Rollers used in tube mills come in various types, each serving a specific purpose:
1. **Forming Rollers**: These are designed to gradually shape the metal strips into the desired tube profile. Forming rollers are strategically arranged in a sequence, each progressively bending the metal until the desired shape is achieved.
2. **Welding Rollers**: After the metal is formed into a tubular shape, it needs to be welded. Welding rollers ensure proper alignment and pressure to achieve a strong bond at the seam where the edges of the tube meet. The precision of these rollers is crucial for high-quality welds.
3. **Finishing Rollers**: Once welding is complete, finishing rollers are employed to smooth out any imperfections, ensuring a uniform, high-quality surface finish for the finished tube.
4. **Support Rollers**: These rollers aid in the smooth transportation of the tube through the mill, helping maintain stability and alignment throughout the process.
The Importance of Roller Quality
The effectiveness of a tube mill heavily relies on the quality and design of its rollers. High-quality rollers can significantly enhance the efficiency and productivity of tube production. Using materials that can withstand high levels of pressure and wear is essential to ensure longevity and reliability. Additionally, rollers with precise diameters and geometries ensure accurate forming and welding, reducing scrap and rework.
Innovations in Roller Design
In recent years, there have been significant advancements in roller technology that have further improved the performance of tube mills. Manufacturers are increasingly investing in materials science, leading to the development of alloyed steel and surface treatments that increase wear resistance and decrease friction. This results in reduced maintenance costs and extended roller life.
Moreover, the introduction of computer-aided design (CAD) and simulation tools has enabled engineers to optimize roller profiles and arrangements. These advancements lead to enhanced accuracy in tube formation and welding processes, which in turn improves the overall product quality.
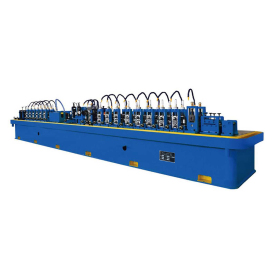
Exploring the Essential Role of Rollers in Tube Mill Operations: Enhancing Efficiency, Quality, and Productivity
Rollers and Energy Efficiency
Energy consumption is a critical consideration in manufacturing processes. Modern roller designs strive to minimize energy usage by enhancing the efficiency of the tube milling process. By reducing friction and optimizing the shaping process, new roller designs contribute to less energy-intensive operations, making the overall machining process greener and more sustainable.
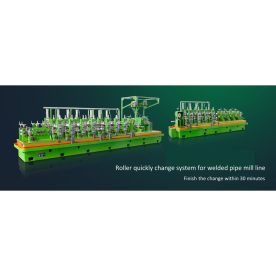
Exploring the Essential Role of Rollers in Tube Mill Operations: Enhancing Efficiency, Quality, and Productivity
Concluding Thoughts
In summary, rollers are much more than simple components in tube mill operations; they are pivotal to achieving optimal results in terms of product quality and operational efficiency. The development of advanced materials and the application of modern engineering techniques have enhanced roller performance, making tube mills faster, more reliable, and more energy-efficient. As industries continue to evolve, the role of rollers in tube mills will undoubtedly expand, promising exciting developments in manufacturing technology and productivity across various sectors. The enduring importance of these components emphasizes that successful production is a smooth ride when rollers are at the helm.High-Speed Cold Cutting Saw Machine