[Pipe mill production line with quality control measures]Enhancing Pipe Mill Production Line Efficiency: Implementing Quality Control Measures for Superior Product Outcomes and Operational Excellence
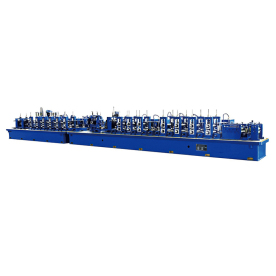
Enhancing Pipe Mill Production Line Efficiency: Implementing Quality Control Measures for Superior Product Outcomes and Operational Excellence
In the modern industrial landscape, the demand for high-quality pipe products is growing. The pipe mill production line is crucial for fulfilling this demand, as it transforms raw materials into finished pipes used across various sectors, including oil and gas, construction, and manufacturing. However, achieving optimal production efficiency goes hand-in-hand with stringent quality control measures. This article explores the significance of quality control in pipe mill production lines and delves into effective strategies to ensure superior product outcomes and operational excellence.
At its core, a pipe mill production line encompasses several stages, including forming, welding, sizing, and testing. Each of these stages presents unique challenges that can impact the final product’s quality. Therefore, integrating quality control measures at every phase is essential to achieving consistency and reliability in the end products. A well-designed quality control system not only mitigates defects but also enhances the overall efficiency of the production process.
One of the first measures to be prioritized in a pipe mill production line is the rigorous inspection of raw materials. The quality of the raw materials directly influences the final product’s performance. Suppliers should be vetted meticulously to ensure that the incoming steel, aluminum, or other materials meet the specified standards. Implementing a robust incoming material inspection protocol, which includes checking chemical composition, mechanical properties, and surface conditions, can significantly reduce the likelihood of defects in the produced pipes.
Once raw materials are deemed satisfactory, the next stage involves forming and welding processes. Here, the importance of quality control becomes even more pronounced. Advanced welding techniques, such as TIG (Tungsten Inert Gas) and MIG (Metal Inert Gas), require precise settings to achieve weld integrity. Employing real-time weld monitoring systems can help ensure that welding parameters are consistently adhered to. Additionally, regular employee training on best practices for welding techniques is essential for maintaining high-quality standards.
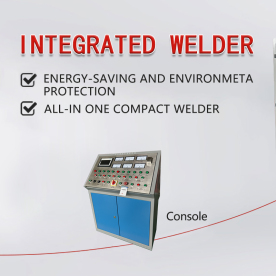
Enhancing Pipe Mill Production Line Efficiency: Implementing Quality Control Measures for Superior Product Outcomes and Operational Excellence
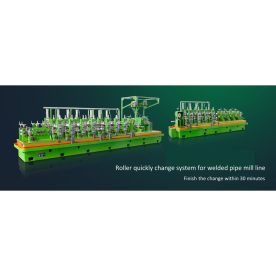
Enhancing Pipe Mill Production Line Efficiency: Implementing Quality Control Measures for Superior Product Outcomes and Operational Excellence
Another critical aspect of quality control in a pipe mill production line is the sizing process. Pipes must meet specific dimensional tolerances to function correctly in their intended applications. Utilizing automated sizing machines equipped with laser measurement technology can provide real-time feedback and corrections, ensuring that every pipe adheres to the required specifications. Additionally, periodic audits of sizing equipment, coupled with routine maintenance, can further enhance measurement accuracy and prevent production errors.
Incorporating non-destructive testing (NDT) is a vital quality control measure that should be integrated throughout the pipe production process. Techniques such as ultrasonic testing, radiographic testing, and magnetic particle inspection can identify internal and external flaws that may compromise the integrity of the pipes. Implementing a scheduled NDT process allows manufacturers to detect and address defects before they escalate, ensuring that quality is maintained throughout the production line.
Beyond the production stage, quality control should extend to the final inspection of finished products. This step often involves visual inspections, pressure testing, and documentation of compliance with industry standards, such as ASTM, ASME, or ISO. These inspections not only guarantee that the pipes meet pre-defined specifications but also provide essential data for continuous improvement efforts. Establishing feedback loops from quality control inspectors to the production team can help identify recurring issues and drive iterative enhancements in the manufacturing process.
Furthermore, adopting modern technological solutions like the Industrial Internet of Things (IIoT) can facilitate comprehensive quality control in pipe mill production lines. With the connectivity of equipment and real-time data collection, manufacturers can analyze production trends, identify potential issues, and optimize operations for better quality outcomes. Such systems not only enhance productivity but also foster a culture of accountability across the workforce.
In conclusion, a successful pipe mill production line hinges on the effective integration of quality control measures at every production stage. From ensuring high-quality raw materials to implementing advanced testing methods, manufacturers can significantly improve product quality and operational efficiency. As industries continue to demand superior pipe products, the importance of robust quality control measures will only grow, making it a critical component of modern manufacturing practices. By prioritizing quality control, pipe mill operators can not only meet market demands but also establish a reputation for reliability and excellence in the competitive landscape.Precision Pipe making equipment